In the spring of 2005 our waste vegetable oil collection had grown to nearly 500 gallons per month, but the introduction of contaminants and water created an emulsified mess. The emulsified oils would sometimes take months to separate. We installed 3 vertical settling tanks for a total of 1100 gallons of storage and despite our best efforts some oils would not separate in a timely fashion. It became clear that we had to find a better way. We began separating our oil using a small "lab" centrifuge similar to what you would find in a medical office (See lab_centrifuge.html for details). This proved that a centrifuge could separate the junk and water from the good oil.
We started shopping for a centrifuge almost immediately, and we learned centrifuges are expensive, and complex machines to install, maintain and run. Nearly all the machines we looked at required three phase power which we did not have. And most vendors we spoke with quoted us machines that started at $25,000 and often suggested machines nearing $50,000.
In the summer of 2005 Mike and I began experimenting and exploring the construction of basic centrifuge specifically for the removal of water and contaminants from waste vegetable oil. Several of these early proto-types resulted in ruined clothes and a thin layer of oil all over the shop. Un phased by our setback, we continued forward. By October of 2005, we had a workable machine that we started to use to clean our oil. We have continued to use this early proto-type to this day. See Visual History below.
At some point in 2006, we discovered that a friend Bud Pitts was selling plans for a centrifuge he modeled after one of our early machines. The machine he built was dimensioned after a scrap billet he purchased from me. His plans are well written and well worth the read. See Farm Show vol. 31, no. 1, 2007 on page 10.
While the design for this machine is very simple, the rotor in such a device carries a lot of potential energy. While an accomplished machinist should be able to fabricate the rotor for the centrifuge, it is not a task to be taken lightly. The construction of rotors from brake drums and pipe steel would ultimately end in failure.
In November of 2006, we started production of precision machine rotors, these are the key device and the most difficult part of the process. This latest bowl generates over 1200 g of force, it is also designed to maintain the full rotational force of the material in the bowl. This bowl maintains over 1000 g force at the inner most lip. Earlier designs focused on large bowl capacities, however these proved ineffective as it was difficult to maintain full rotational force of the material and the narrower inner lip decreased the g force by over 50% at the inner lip.
In January 2007 we launched our web site. Our goal is to make available a complete machine in the next few months. We're making the bowls available now to assist those who have purchased plans to complete their machines.
Visual History of our development from the beginning (Images are clickable)
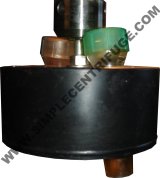 |
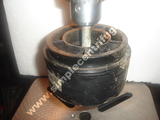 |
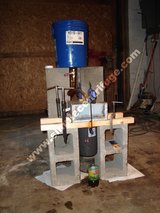 |
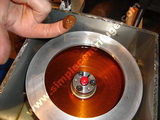 |
This is our first centrifuge attempt, the "Lab Centrifuge" from July 2005. We have a page devoted to this here. |
This is our first bowl centrifuge from August 2005. Pipe fittings on the drill press but it proved it would work. This rotor only processed about 2 gallons of our nastiest oil. We knew we had a winner idea. |
This is our first machine from October 2005. The housing was too small, lacked seals, and the splash wall but it worked! Those items would come later. |
This is a rare photo from the first machine. Look at the water droplets it collected. It worked well. |
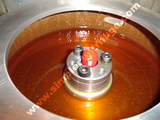 |
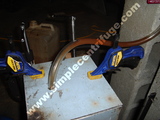 |
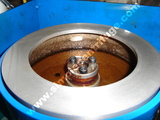 |
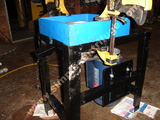 |
If any picture shows what the centrifuge can do this is it. |
This picture shows what the oil looked like going in. It was amazing. |
Soon after we built a new housing from steel plate. This has proven to be a very durable and flexible housing. |
In May 2006 we water tested our belt drive version of the centrifuge. It was based on a table saw arbor. At 6900 RPM this machine does over 5000g. We used this for 6 months. |
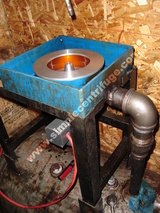 |
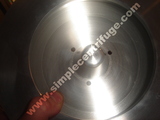 |
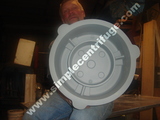 |
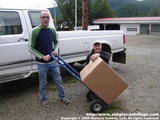 |
In October 2006 we switch back to the direct drive with our new rotor design. |
In January of 2007 we introduced the self draining bowl. This has been a huge time saver. This is a photo of our new three hole design. |
In May 2007 we completed the patterns for our cast body, lid, and legs. With all plumbed inlets and Viton seals it should prove wonderful. No more leaking oil all over the garage. |
Happy 4th of July, 2008. Mike and I get ready to load our first turnkey machine. This machine is going to Trout Lake, Washington. Turnkey machines now available. |
More photos are available in the gallery. |